Cooling system
Atualmente um grande desafio enfrentado em sistemas eletrônicos é o aquecimento de seus componentes em decorrência do acréscimo na intensidade de corrente elétrica proveniente da implementação de novas funções e do funcionamento simultâneo de subsistemas. Aplicando esse contexto ao BlueROV2 operado pela equipe, a conversão deste em um AUV exigiu o desenvolvimento de um novo dispositivo de resfriamento para a unidade de processamento Raspberry instalada, visto que o superaquecimento desta a temperaturas acima de 65 ºC implicava em redução crítica da autonomia do veículo, impedindo a realização das atividades designadas, bem como a redução da vida útil do componente devido ao ciclo térmico de trabalho ao qual era submetido.
Frente a esses problemas, inicialmente realizou-se a análise da capacidade inicial de dissipação do casulo e o levantamento das características desfavoráveis ao arrefecimento do sistema. No qual observou-se que a troca térmica era realizada via convecção livre com o ar dentro do casulo. A baixa condutividade térmica do ar e das paredes poliméricas do casulo, juntamente com a ineficiência da convecção livre na troca de calor implicam em grande resistência térmica entre os componentes eletrônicos e o ambiente externo. Assim, era fundamental à eficácia do projeto que essa resistência fosse reduzida.
A partir disso, foram elencadas algumas restrições e critérios de seleção, sendo eles:
- Dificuldade de reposicionamento de componentes e restrição espacial;
- Preservação de integridade estrutural e estanqueidade do casulo;
- Restrição de recrutamento energético;
- Redução de ruído eletromagnético.
Solução do arrefecimento
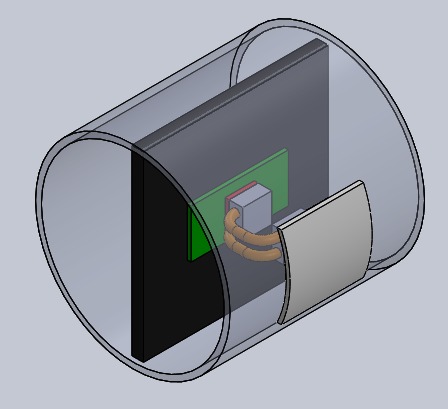
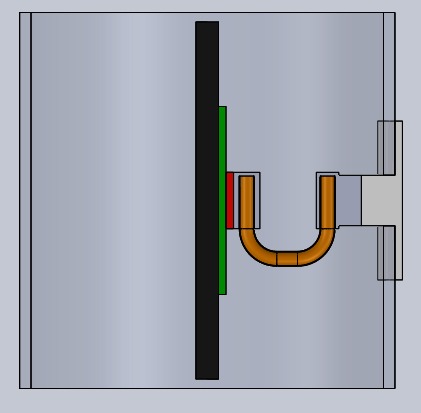
A partir das restrições do projeto a equipe definiu as características finais do dispositivo de controle térmico a ser implementado no AUV. No qual concluiu-se que sobre o processador Raspberry será montada uma base condutora, aderida via pasta térmica. Desta base, o calor produzido será conduzido por um heat pipe até o dissipador, componente condutor instalado através da parede do casulo. O acoplamento do heat pipe ao dissipador será também feita através de uma base condutora. A interface dessa montagem será preenchida com um adesivo epóxi térmico. Observada a baixa condutividade térmica desse adesivo em relação aos materiais metálicos do conjunto, o ajuste dimensional do acoplamento será tal que, ainda garantido a adesão, minimize a resistência térmica na interface.
A fim de evitar a transferência de calor via convecção natural interna pelo ar na vizinhança dos componentes, toda a superfície do conjunto (bases, heat pipe e dissipador) exposta ao ar interno será enclausurada por um filme isolante. Recobrando a discussão realizada na restrição 2, a eficácia e eficiência do dispositivo estão atreladas à proporção do calor conduzido através do conjunto em relação ao transferido ao ar interno ao casulo.
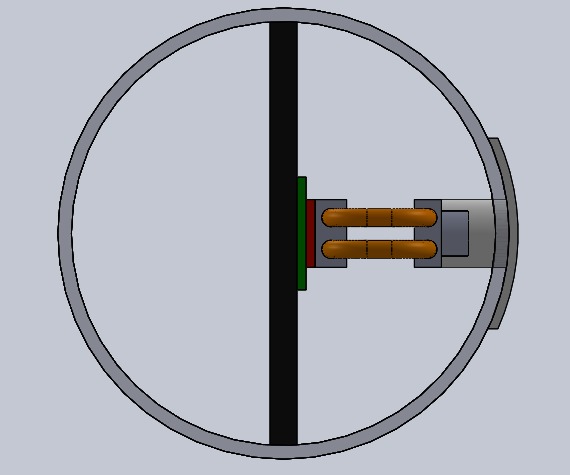
Visto que o dissipador será montado através da parede da estrutura, existe a preocupação com concentração de tensões e estanqueidade após instalação. A solução encontrada pela equipe então consiste na usinagem de um único furo circular na parede, evitando geometrias com arestas agudas e a montagem do dissipador a partir do tratamento da superfície da interface com um primer e aplicação de um selante polimérico, similar ao utilizado na indústria automotiva na adesão de vidro a componentes metálicos.